News
Differences Between Hot Rolling and Cold Rolling
Optimizing steel properties for specific applications involves more than altering its chemical composition. Rolling is a critical process used to enhance steel’s shape, uniformity, and mechanical performance. Rolled steel is broadly categorized into two types: cold-rolled steel and hot-rolled steel, each with distinct characteristics suited for different applications.
What Is Hot-Rolled Steel?
Hot rolling refers to steel production under extreme heat treatment—typically at temperatures above 926°C (1700℉). The process begins with heating large rectangular metal blocks (slabs or billets) to a molten state before pressing them into sheets or coils. The steel is then cooled naturally, forming its final shape.
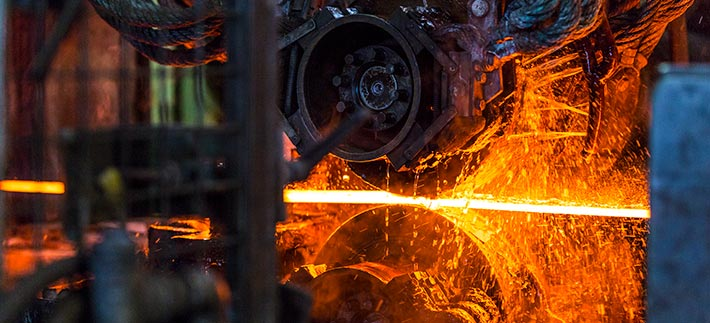
What Is Cold-Rolled Steel?
Cold-rolled steel is essentially hot-rolled steel subjected to further processing. After cooling, the steel undergoes additional steps at room temperature, such as rolling, grinding, or polishing, to refine its dimensions and surface finish. The term "cold rolling" applies to steel shaped through compression-based techniques like cold-rolling mills or press brakes. This process enhances dimensional accuracy and strength.
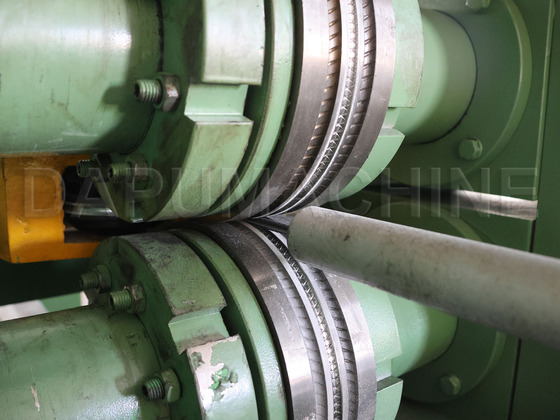
Hot-Rolled vs. Cold-Rolled Steel: Key Comparisons
Category |
Hot-Rolled Steel |
Cold-Rolled Steel |
Process |
- Rolled at high temperatures (≥926°C/1700℉) |
- Further processed from hot-rolled steel |
Characteristics |
- Rough surface with mill scale |
- Smooth, oily surface |
Advantages |
- Low cost (fewer steps) |
- High surface finish |
Disadvantages |
- Dimensional defects (expansion/shrinkage) |
- Higher cost (additional processing) |
Key Performance |
- Better ductility |
- Higher hardness and strength |
Common Applications |
- Automotive frames, wheel rims |
- Aerospace parts, precision machinery |
Priority Use Cases |
Cost-sensitive applications with relaxed tolerances |
High surface quality, precision, or strength requirements |
Additional Differences
1. Rolling Temperature
Hot rolling: Performed within the steel’s recrystallization range (750–1300°F) to reduce forming resistance.
Cold rolling: Relies on plastic deformation at room temperature, often requiring annealing to relieve stress.
2. Weldability
Hot-rolled steel: Easier to weld due to low carbon content and uniform microstructure, though post-weld treatments may be needed.
Cold-rolled steel: Prone to cracking from work hardening; pre-treatment (e.g., annealing) is often necessary.
3. Economic Considerations
Hot-rolled steel: Ideal for large-scale, low-complexity components (e.g., beams, rails).
Cold-rolled steel: Used for high-value products (e.g., precision instruments, decorative materials).
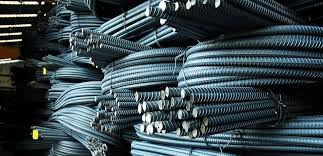
Tianyi High-Tech Carbide Roll Rings are widely used in steel mill stands to assist in producing hot- or cold-rolled steel, including high-speed wire rods. Custom solutions are available to meet diverse industrial needs.
Related product categories
- long-life roller rings for steel industry
- benefits of using cemented carbide roll rings for high-speed rolling
- thermally stable carbide rolls for steel industry
- corrosion-resistant carbide rolls for cold rolling mills
- custom-manufactured roll rings for high-temperature applications
- improve rolling mill efficiency for bar mills
- rolling mill roller rings Mexico
- best carbide roll rings Brazil
- carbide roll rings with tight tolerances Iran
- 0.3 to 30mm tungsten bars/rods
- china tool bit
- china ceratizit solid carbide rods